Production
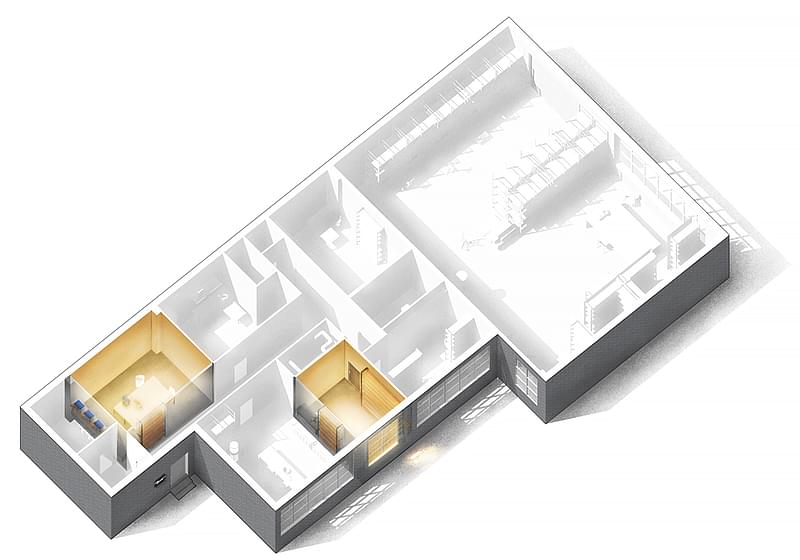
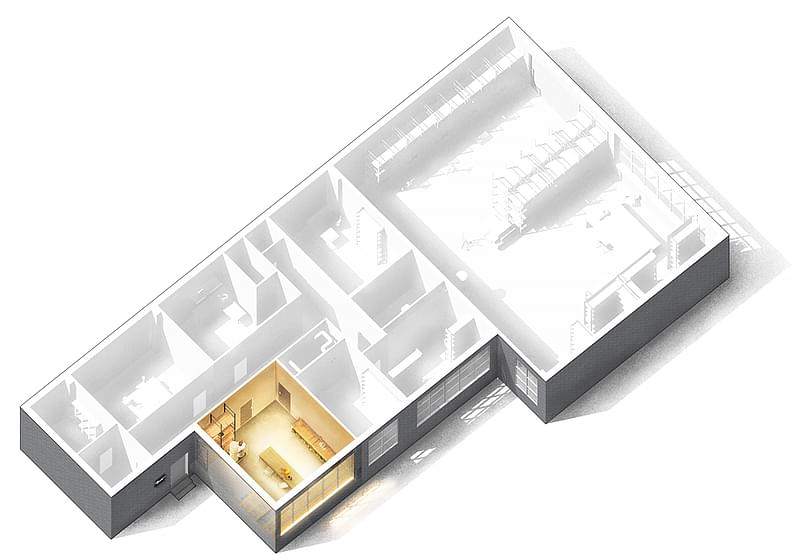
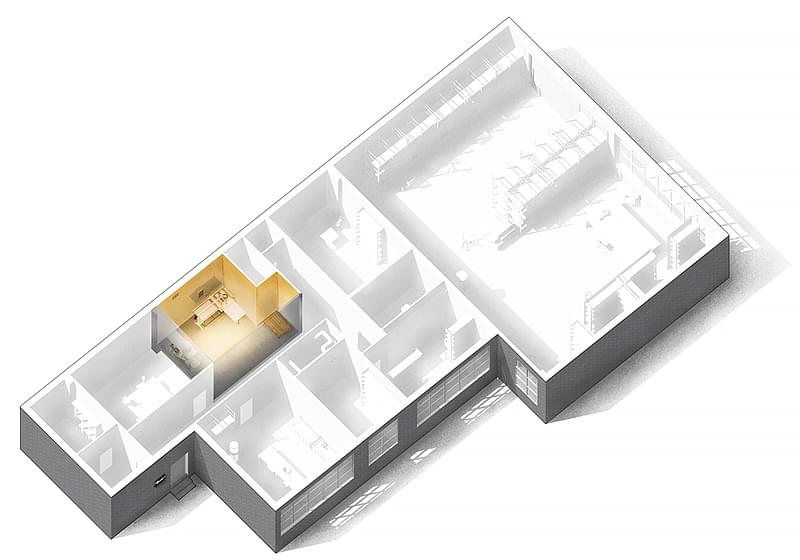
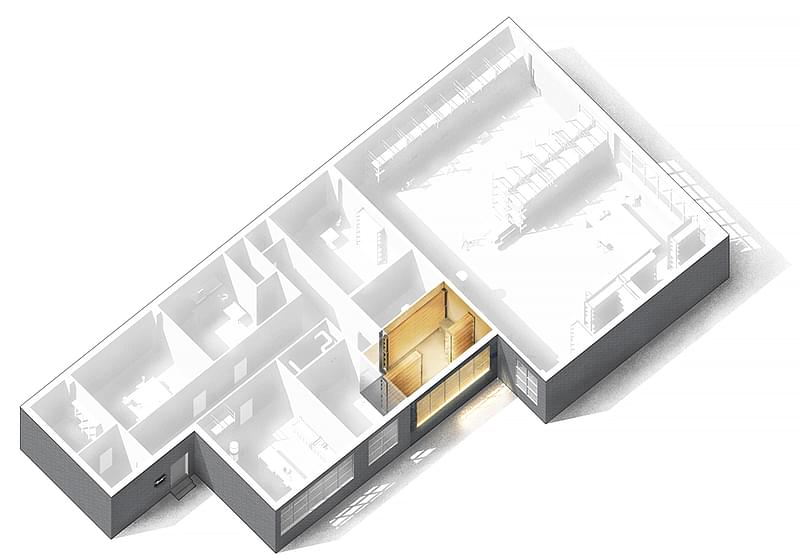
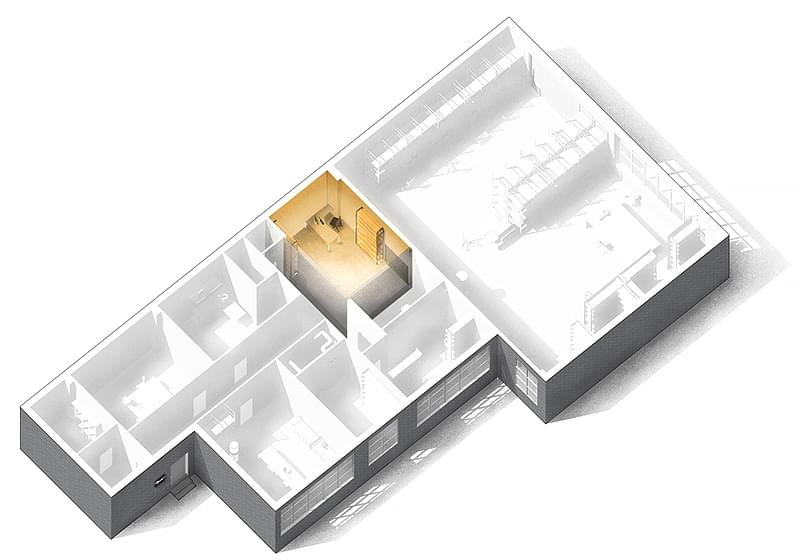
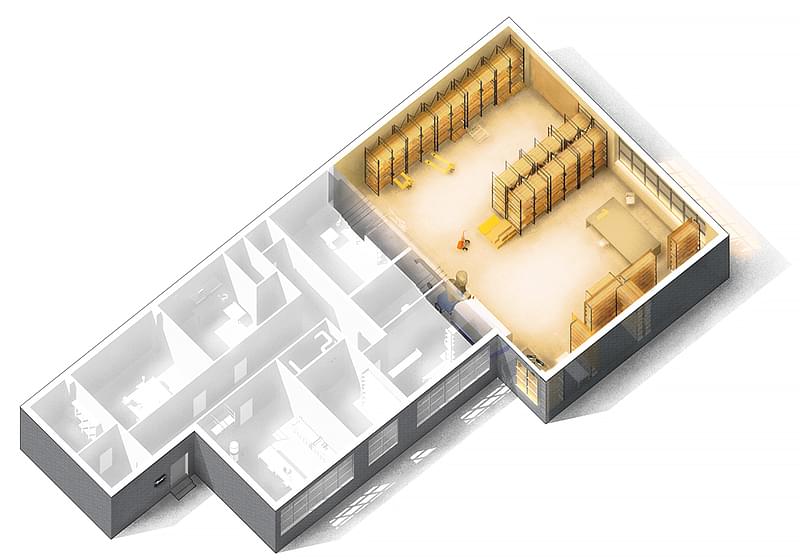
Modeling and design
The main purpose of our brand is to produce lighting equipment that combines professional technical content and laconic design.
The launch of every new series of luminaires into production starts with a detailed study of the design features of the future luminaire, creation of technical documentation and three-dimensional model.
According to the design drawings and 3d model, the master makes the first prototype of the product. After testing the prototype, the luminaire models are put into serial production.
Polishing, restoration and repair of models are also ensured by the masters of the modeling department.
-
2 months of preparation were required to launch the first large-sized luminaire into production
-
5 luminaire models were developed exclusively for interior design projects.
-
After 2-3 cycles of use, the master model needs to be restored.
Casting of housings
Making a plaster housing is one of the most important tasks for our production. We need to get a solid and uniform structure of the housing. The master strictly adheres to the technology of casting and demolding, taking into account a number of aspects: thermal conditions, air humidity level, composition of the plaster mixture, water quality, degassing parameters, time intervals, etc.
After polishing, the plaster bodies are subject to manual quality inspection and enter the drying chamber.
-
Up to 150 housing can be produced daily.
-
More than 120 kg of plaster and 35 liters of water are required for one working day.
-
It takes at least 72 hours to dry one housing.
Grinding of housings
Dried and tested housings are delivered to the grinding shop. On the grinding line, the master removes the technical layer of plaster (overflow). Then he performs a fine grinding with a fine abrasive, bringing the housing to its final state. At this stage, the housings are visually inspected in regards to any defects, chips or cracks.
-
4 kg of gypsum dust is collected daily in the dust collector of the exhaust system.
-
The air in the room is renewed 3 times per hour thanks to the recirculation system.
-
4 various types of abrasive surfaces are used in grinding.
Assembly of electronic components
We develop and produce light modules ourselves, taking into account the characteristics of each series of luminaries, and complete them with professionally selected transformers. This enables ensuring full quality control of the elements and their assembly.
We check faultlessness and correctness of LED operation, performance of power supplies at extremely high loads, reliability of soldering SMD components, purity and light transmission of the diffusers, electrical insulation of the wires, uniformity of light emission by the module, and much more.
The assembly culture that we have allows creating products of high-quality standards and ensuring prompt production times.
-
648 LEDs are required to manufacture D550 LED module.
-
275 mg of glue is used to solder one D100 diffuser to the luminaire housing.
-
180 sets of wires can be made by a master in one work shift.
Technical control department
Creation of a high-quality product is an important principle of our production.
We have developed and implemented a production technology, comprising: incoming quality control of all components, multi-stage inspection of manufactured units and a system for final control of finished products.
Thanks to the proven technology, only those products quality thereof leaves no doubt, are delivered to the packing area, thus we can provide a 5-year warranty for all our equipment.
-
Every luminaire produced is subject to more than 9 control operations.
-
5% of the products is not subject to internal technical inspection and is disposed of.
-
The share of complaints is less than 1% of the total volume of products made in five years.
Packaging area and warehouses
The products ready to packaging and further shipment is delivered to the final stage. With the help of laser equipment, we apply technical markings and date of manufacture of electronic components, and prepare a set of packaging for the luminaire.
For every series of luminaires, individual packaging has been developed, taking into account the specific features of transportation of every component of the luminaire. The packaged luminaries are delivered to the finished product warehouse.
-
15 liters of air is required to pack the Orby luminary.
-
5 layers of packaging is used for large-sized luminaires.
-
More than 2 tons of plaster luminaire housings are in the warehouse of assembly parts.